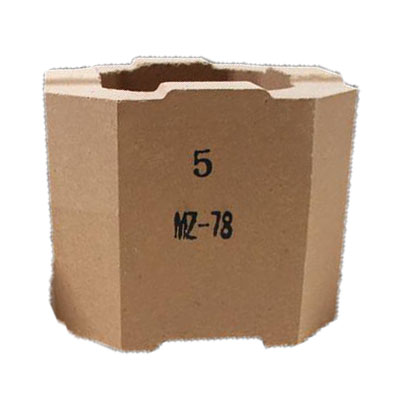
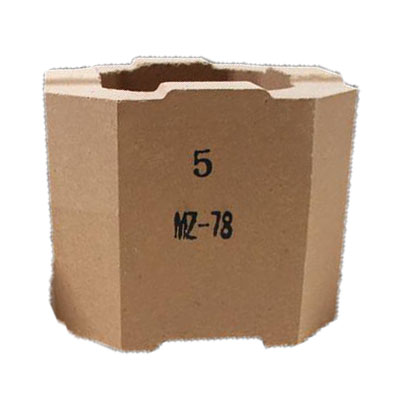
Refractory magnesia zirconium bricks
Model Number: Hongtai
Certification: ISO9001
Minimum Order Quantity: 1 Ton
The production process of magnesia zirconium brick
There are basically three process routes for the production of magnesia zirconium bricks.
1) Using magnesia-zirconium sand as raw material to produce materials with uniform distribution of MgO and ZrO2. This type of material consists in first synthesizing magnesia-zirconium sand. It is obtained by mixing MgO and ZrO2 raw materials according to requirements - fine grinding - forming into balls (blank) - sintering/electric melting to obtain sintered/fused magnesia-zirconium sand. Then the magnesia-zirconium sand is crushed—classified—batched—mixed—formed—sintered to obtain ZrO2 composite magnesia refractory with uniform MgO/ZrO2 distribution. It can be seen that their production process is the same as that of magnesia refractories.
2) ZrO2 is combined with magnesia to produce magnesia-zirconium bricks. The production method of this type of material is to mix ZrO2 into magnesia to produce ZrO2 composite magnesia refractories with different MgO/ZrO2 ratios.
Their production process is basically the same as the production of magnesia-chromium refractories.
3) Special magnesia zirconium bricks. The difference between the production process of this type of material and the ordinary magnesia refractory is that the surface of the magnesia refractory aggregate particles is coated with a refractory material with ZrO2 as the main component, and the surface of each particle is uniformly formed into a thin film. The ZrO2 coating is dried and fired to form a solid ZrO2 sintered layer between the periclase particles. This product has very good performance. The material does not produce cracks, cracks, and peels during use, and has good thermal stability.
The magnesia-zirconium brick with the addition of 20% of ZrO2·SiO2 actually belongs to the MgO-2MgO·SiO2-ZrO2 series refractory material. The high corrosion resistance of the bonded matrix layer in the material, the corrosion resistance of this brick has been proven in the use of regenerators and melting chambers. Since its first use, this material has shown good performance in the condensation zone for 10 years, making it possible to use it in the upper part of the regenerator and even in the vault.
A manufacturing method of continuous casting upper nozzle brick is to mix and knead a mixture of non-spherical sintered or fused magnesia (70% to 99%) and zirconia powder (30% to 1%) with a particle size of less than 1 mm, and shape After being fired, zirconia powder can be replaced by chrome stone powder. When 100% of the mixture is added with 20% or less of silicon oxide raw material fine powder (calculated as SiO2), the peeling resistance can be improved. In addition, the continuous casting nozzle brick produced by the above method also has good corrosion resistance and high temperature strength.
The use of magnesia zirconium brick
Used in glass kiln regenerators and in the steel industry.
Physical and chemical analysis
Production capacity: Our factory actively response to government environmental protection policy, we designed and built the fully automatic controlled high temperature gas tunnel kiln (1700℃), and got capacity of annual output 70,000 tons of high quality refractory products.




Packing details:
★Bricks: Fumigated wooden pallet with log paperboard covered and stainless steel band strapping, the whole outside is wrapped with thermoplastic film. Or carton packaging.
★Wooden pallet size: usually 92*92cm (standard brick)
★Castable: Ton bag with rain film and 25kg bags inside
★Or according to customer’s requirements




Transportation
★Port of dispatch: Tianjin port; Qingdao port
★Delivery time: According to customer’s demand or two sides negotiate




We provide you
★Timely response: Timely response to your inquiry within 24 hours and provide solution.
★Competitive Price: Make the products competitive in your market.
★Free sample: Free sample are offered, trial order are accepted for quality evaluation.
★Strict quality control: We set Quality Management System, from the raw material to finished products, produce high quality products according to chemical & physical specifications strictly to satisfy customers’ needs.
★Fast delivery time: Within 3-30 days according to your quantity after receiving your advance payment.
★ Professional services: Provide pictures from order to delivery. Inspect report by our country’s designated authority and oversea services if necessary.
We are here for you!




Certification: (ISO 9001:2015)
Please Feel free to give your inquiry in the form below. We will reply you in 24 hours..