Although simple magnesia refractories are widely used, they have some inherent weaknesses, such as large thermal expansion coefficient, poor thermal shock resistance, easy moisture absorption and hydration, and slag penetration into the bricks, resistance to thermal spalling and structural spalling. Not good. The addition of zirconium (ZrSiO4) composite magnesia refractories overcomes these weaknesses. By introducing ZrO2, the low melting point can be islanded without forming a continuous liquid phase, which improves the material's resistance to penetration. And resistant to erosion.
1 test
1.1 Raw materials
High-purity magnesia, fused magnesia and zircon sand are used as the main raw materials.
1. 2 Preparation of samples
The zircon bricks are directly added into the magnesia, and the magnesia-zirconium bricks are produced according to the ordinary magnesia brick process. The ratio of the zircon and magnesia mass percentages is 95:5.0, 90:10, 85:15, 80:20, 75, respectively. : 25, 70:30. Using 3 grade ingredients, the critical particle size is 4mm, the coarse and medium fine particles are matched according to the principle of the closest packing, and the composite binder of the pulp slurry is added. The mixture was evenly mixed and made into 230 mm × 115 mm × 65 mm standard bricks on a 630 t friction brick machine with a brick density of >3.1 g·cm-3. After drying, it is placed in a high-temperature tunnel kiln with natural gas as fuel, and fired at 1560, 1580, and 1600 ° C, respectively.
2 Results and discussion
2. 1 room temperature physical properties of magnesium zirconium brick
Click to open the original image
The effect of the amount of zircon added on the apparent porosity, bulk density and compressive strength is shown in Fig. 1, Fig. 2, and Fig. 3.
It can be seen from the figure that as the temperature increases, the bulk density of the magnesium zirconium bricks gradually increases, and the apparent porosity decreases gradually, while the compressive strength is highest at 1580 °C. This is because there are many fine cracks on the surface of the magnesium zirconium brick at 1600 ° C, and there is a phenomenon of over-burning (large shrinkage, small amplitude distortion), resulting in a decrease in strength. Therefore, the physical properties of the firing at a temperature of 1580 ° C reached an optimum value.
As the amount of zircon added increases, the bulk density and compressive strength first increase and then decrease, while the apparent porosity decreases first and then increases. This is because with the increase of zircon content, MgO and SiO2 decomposed from ZrSiO4 have a higher melting point (1890 °C), and the content of forsterite 2MgO·SiO2 (M2S) is gradually increased, and the performance of bricks is gradually enhanced. . When the addition amount of zircon is 20%, the performance is the best. When the content exceeds 20%, the performance begins to decrease. This is because the SiO2 decomposed by ZrSiO4 starts to be excessive, and the excess SiO2 forms a low-melting silicate phase, so that the system liquid As the phasor increases, the physical properties of the bricks gradually decrease.
2. 2 load softening temperature
Figure 4 shows the relationship between the load softening temperature and the amount of zircon added. It can be seen from the figure that as the amount of zircon sand increases, the load softening temperature first increases and then decreases. When the zircon sand is 20%, the load softening temperature is the highest. At this time, the load softening temperature is >1700 °C because a large amount of melting point is formed. The higher (1890 °C) forsterite 2MgO·SiO2 (M2S); and the ZrO2 decomposed by ZrSiO4 promotes the growth of the main crystal phase, the character development is more perfect, and the viscosity of the high temperature liquid phase is increased, resulting in silicate phase. It exists more in isolation at the junction of high temperature solid phase, enhances the direct bonding rate of high temperature solid-phase forsterite (M2S) in the matrix, and improves the microstructure in the matrix, thereby increasing the load softening temperature of the magnesium zirconium brick and its Resistance to erosion.
The load softening temperature is the ability to characterize the high temperature and constant load of the brick during continuous heating, and also to some extent the structural strength and creep properties of the brick under the conditions of use. In practical application, the magnesium zirconium brick is built in the middle of the lattice of the glass kiln regenerator. The higher load softening temperature is better for bearing the load of the upper lattice brick, buffering thermal stress and mechanical stress, and ensuring the safe and stable operation of the lattice. value.
2. 3 thermal shock resistance
Figure 5 shows the relationship between thermal shock resistance and the amount of zircon added. It can be seen from the figure that the thermal shock resistance of zircon is 15% and 20%, which is 6 times. This is due to the ZrO2 composite material. During the post-burning cooling process, part of t-ZrO2 will be converted into m-ZrO2, and the volume expansion and shear strain accompanying the phase transformation will cause a large number of microcracks and micro-surrounds around m-ZrO2. The crack nucleus absorbs or releases part of the energy of the main crack when these microcracks are in the action zone of the main crack front end, increases the energy required for the main crack propagation, reduces the stress concentration at the front of the main crack, and inhibits the expansion of the main crack. , thereby improving the toughness of the material.
2. 4 Image analysis of magnesium zirconium brick
Fig. 6 and Fig. 7 are XRD patterns and SEM photographs of magnesium zirconium bricks fired at 1580 ° C, respectively. It can be seen from Fig. 7 that a large amount of forsterite (M2S) is formed after firing, and the mark on the SEM photograph shows that the gray periclase (1-MgO) grains are basically isolated, the crystal form is well developed, and the boundary is clear. The intergranular cementation phase is mainly light gray forsterite (3,4-M2S), forsterite is used as the binding phase, and the periclase-pericite is combined, and the white spherical zirconia (2-ZrO2) Uniformly distributed between the periclase, the degree of direct bonding between the phases is very good, greatly improving the corrosion resistance of the magnesium zirconium brick.
3 Conclusion
(1) With the increase of the amount of zircon added, the bulk density, compressive strength, load softening temperature and thermal shock resistance first increase and then decrease, while the apparent porosity decreases first and then increases, zircon sand The performance reaches a maximum when the amount is 20%;
(2) The addition amount of zircon sand is 20%, and the comprehensive performance reaches the optimum value when the firing temperature is 1580 °C;(3) The zirconium-zinc brick obtained by adding 30% zircon sand has high load softening temperature, good corrosion resistance and thermal shock resistance, and is very suitable for use as a lattice brick of a glass kiln regenerator.
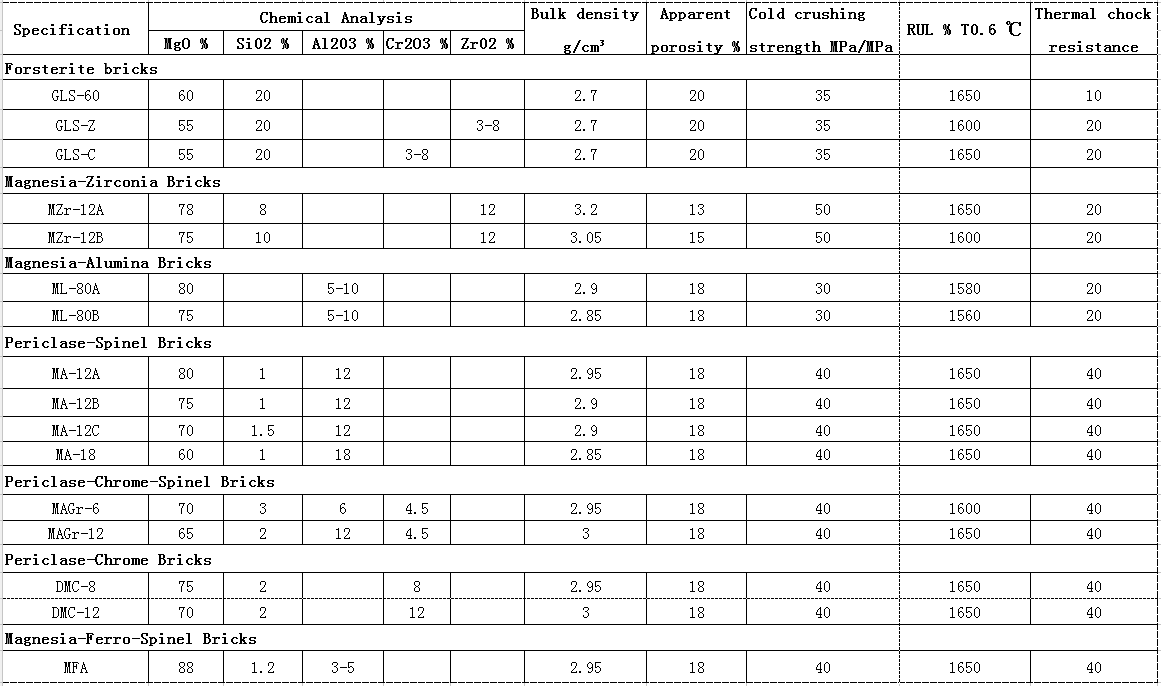